As an aficionado of metallurgy, the world of carbon steel is a fascinating universe to explore. A simple change in the carbon content can significantly alter the properties of steel. Notably, the 1055 and 1095 carbon steel grades have piqued the interest of many, due to their distinct properties and applications.
The difference between 1055 and 1095 carbon steel lies in their carbon content, which directly influences their strength, durability, and cost. In short, 1055 has a lower carbon content making it more ductile and affordable, while 1095 has a higher carbon content offering superior hardness and edge retention, but at a higher price point.
This disparity may seem minor, but it has profound implications for those deciding between the two. For knife makers, engineers, or anyone needing steel with specific properties, making the right choice between 1055 and 1095 can make a substantial difference in their end product.
Understanding Carbon Steel
Definition of Carbon Steel
Carbon steel is an alloy made primarily of iron and carbon. The proportion of carbon in the mixture has a significant influence on the steel’s properties. Its percentage is what defines the type of carbon steel: low, medium, or high.
Importance of Carbon Content
The carbon content determines the steel’s hardness, tensile strength, and ductility. The more carbon a steel alloy has, the harder and stronger it becomes but loses its ductility. Conversely, lower carbon content makes steel more ductile and easier to work with but less hard and strong.
The 1055 Carbon Steel
Detailed Overview
The 1055 carbon steel is a medium carbon steel with about 0.55% carbon content. This composition gives it a good balance between strength and ductility, making it a versatile choice for various applications.
Characteristics and Benefits
1055 steel is relatively easy to work with due to its lower carbon content. It has good ductility, meaning it can be bent, cut, and shaped without breaking. Additionally, it offers decent hardness and tensile strength, suitable for many general-purpose uses.
Ideal Uses and Applications
Given its balanced properties, 1055 carbon steel is used in making a range of items, from springs and cutting tools to swords and axes. Its versatility is a significant advantage, especially for manufacturers needing a reliable, all-round steel grade.
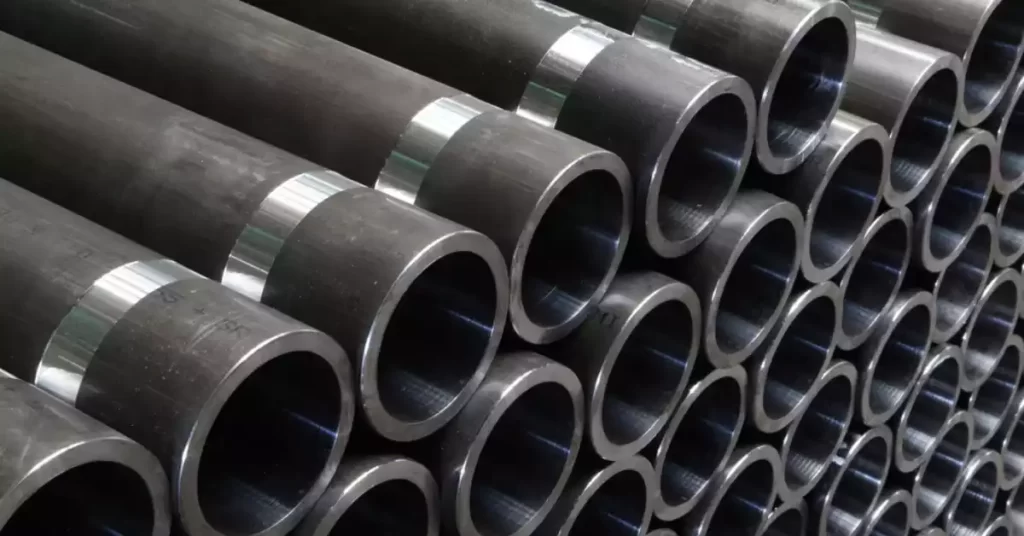
The 1095 Carbon Steel
Detailed Overview
Contrarily, the 1095 carbon steel is a high carbon steel variant with about 0.95% carbon content. It’s known for its hardness and excellent edge retention, though it compromises on ductility.
Characteristics and Benefits
1095 steel is harder and more brittle compared to 1055. It offers superior edge retention, making it an excellent choice for items that need to hold a sharp edge for extended periods. However, its higher carbon content makes it more challenging to work with, and it requires careful handling to prevent breakage.
Ideal Uses and Applications
Due to its high hardness, 1095 carbon steel is a favorite for knife makers and blade smiths. It’s commonly used in high-quality knives, razors, and other cutting tools. While it’s not as versatile as 1055, it excels in applications requiring superior cutting performance and edge retention.
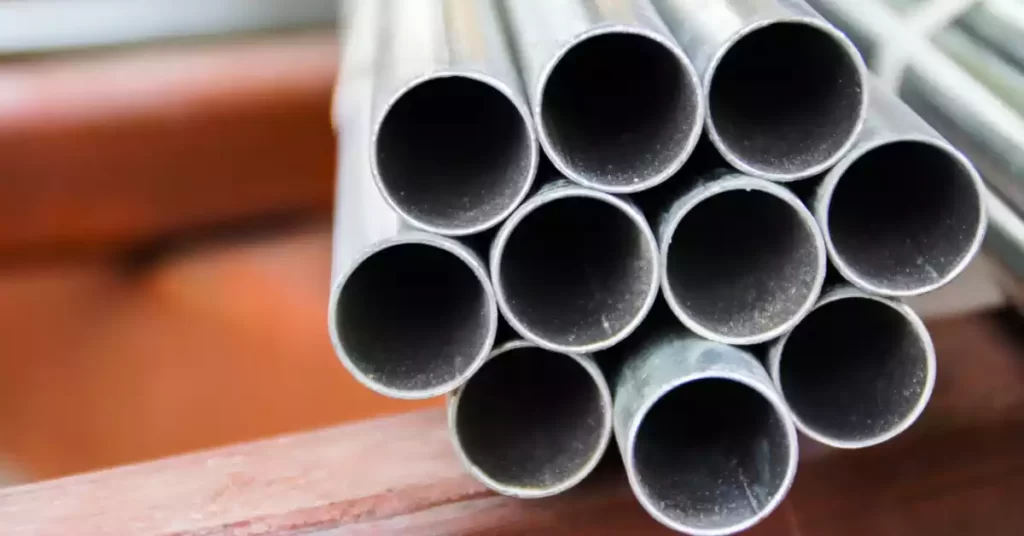
Differences Between 1055 and 1095 Carbon Steel
Comparison of Composition
At the heart of the 1055 and 1095 carbon steel lies their carbon content. The 1055 carbon steel, as its nomenclature suggests, contains 0.55% carbon, whereas the 1095 carbon steel carries a substantially higher carbon content of 0.95%. This differential plays a major role in deciding their properties and applicability.
Performance Differences
The variation in carbon content between the two types of steel yields contrasting performance characteristics. 1095, with its high carbon content, offers exceptional hardness and edge retention. It’s an ideal choice for tools and implements where maintaining a sharp edge under rigorous use is paramount.
In contrast, the 1055 grade, having a lower carbon content, is more malleable. This makes it a more versatile material, capable of being manipulated into various forms without losing its integrity. Although it might not hold an edge as long as the 1095, its superior ductility makes it a suitable choice for applications demanding resilience under pressure or impact.
Durability and Hardness Comparisons
The hardness of steel is often correlated with its durability – the harder the steel, the longer it tends to last. However, hardness comes with a trade-off. While 1095’s superior hardness lends it excellent durability under controlled conditions, it’s more prone to chipping or breaking when subjected to high-impact or flexing tasks due to its increased brittleness.
On the flip side, 1055, despite being less hard, might fare better under high-stress applications. It can absorb and distribute force more effectively due to its increased ductility, reducing the likelihood of catastrophic failure.
Cost Differences
The cost of steel is influenced by several factors, including its carbon content. Generally, higher carbon steels tend to be more expensive due to the increased processing and handling requirements. Consequently, 1095 carbon steel is usually more costly compared to the 1055 variant. For large-scale or budget-conscious projects, the cost-effectiveness of 1055 might be a more appealing proposition.
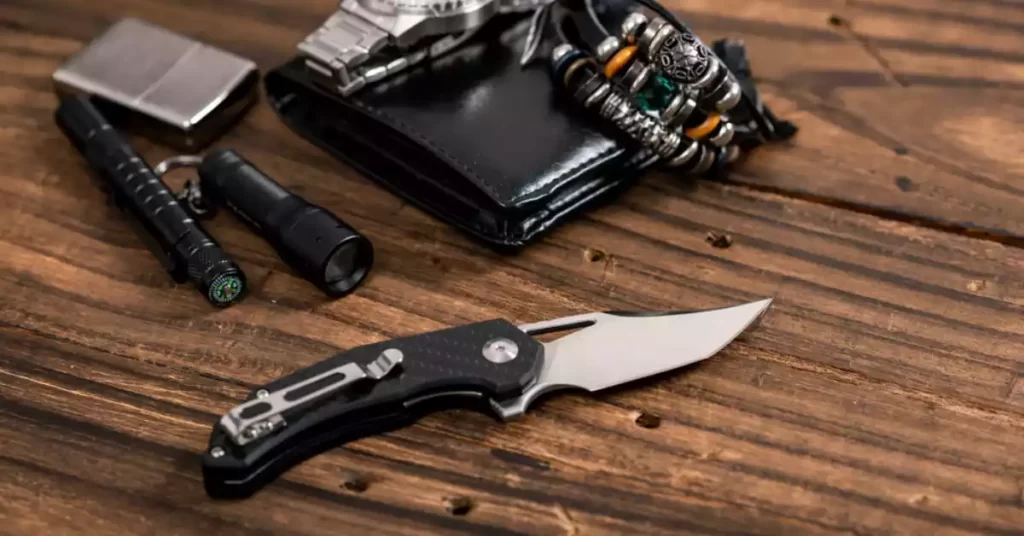
User Experience: 1055 vs 1095
Personal Experience with 1055
In my journey through the world of metals, 1055 carbon steel has always come across as a dependable choice. Its versatility and affordability make it an excellent starting point for beginners venturing into metalworking or DIY enthusiasts looking to create robust tools or implements.
Personal Experience with 1095
In contrast, my experience with 1095 carbon steel has been more nuanced. Its excellent edge-holding capabilities make it a favorite for crafting high-quality blades and cutting tools. However, the demanding handling and maintenance requirements could prove challenging for those not acquainted with high-carbon steel care routines.
Tips for Choosing Between 1055 and 1095
Consideration Factors
Selecting between 1055 and 1095 carbon steel isn’t a simple black-or-white decision. It requires careful consideration of several factors, including the intended application, available budget, fabrication facilities, and maintenance capabilities.
When to Choose 1055
If your project involves creating tools or objects that demand flexibility and resistance to impact, or if you’re working with a tight budget, 1055 might be your best bet. Its affordability, coupled with its well-rounded performance characteristics, makes it an excellent all-rounder.
When to Choose 1095
In contrast, if your project involves creating cutting tools or blades where sharpness and edge retention are paramount, 1095 would be a more suitable choice. Though pricier and more demanding to work with, its superior performance in edge-centric applications makes it worth the investment.
Frequently Asked Questions
Is 1055 or 1095 steel better for making knives?
The choice between 1055 and 1095 for knife-making depends on the specific requirements of the knife. If the primary need is for a hard, sharp blade that maintains its edge, 1095 would be the better choice. However, for larger knives or those expected to endure heavy use or impact, the greater resilience of 1055 might be more suitable.
Can 1055 steel be hardened like 1095 steel?
While both 1055 and 1095 can be hardened, 1095 can achieve a higher level of hardness due to its greater carbon content. However, it’s important to remember that increased hardness comes at the expense of ductility and toughness – hardened 1095 steel is more likely to be brittle and may chip or break under high impact.
How do 1055 and 1095 carbon steel respond to rust?
Both 1055 and 1095 carbon steels are prone to rust if not properly maintained. They lack the chromium content found in stainless steels that provides rust resistance. Therefore, knives or tools made from either of these steels should be kept dry and clean, and regularly oiled to protect against corrosion.
Conclusion
Choosing between 1055 and 1095 carbon steel hinges on understanding their unique properties and how they align with your project’s requirements. The contrast in carbon content influences their hardness, ductility, and cost – determining their suitability for different applications.
1055, with its lower carbon content, offers an affordable and versatile option for tasks requiring ductility and resilience. In contrast, the high carbon 1095 grade excels in delivering sharp, durable edges for cutting tools but at a higher cost and increased care requirements.
Whatever your project might be, remember that knowledge is the key. Understanding the inherent characteristics of these steel grades will empower you to make an informed choice, helping bring your vision to life in the best way possible.