Ever wondered if it’s possible to anodize stainless steel to give it a vibrant, colorful finish? You’re not alone. Anodizing is a popular process for coloring aluminum, but many are curious about whether it can be applied to stainless steel.
In this comprehensive guide, we’ll delve into the world of anodizing, explore the properties of stainless steel, and discuss the possibilities and limitations when it comes to applying this process to this corrosion-resistant material.
Understanding Anodizing
Anodizing is an electrochemical process that forms an oxide layer on the surface of a metal, typically aluminum.
This oxide layer offers enhanced corrosion resistance, increased surface hardness, and the ability to accept a wide range of colors through dyeing.
The process involves immersing the metal in an electrolyte solution and passing an electric current through it, which causes the formation of an oxide layer.
Stainless Steel: Characteristics and Composition
Stainless steel is an alloy primarily composed of iron, with chromium, nickel, and other elements added to enhance its corrosion resistance, strength, and other properties.
The presence of at least 10.5% chromium in stainless steel forms a protective oxide layer on the surface, which prevents further corrosion.
Stainless steel is known for its durability, low maintenance, and excellent resistance to staining and rust.
Can You Anodize Stainless Steel?
While anodizing is a popular and effective method for treating aluminum, it is not suitable for stainless steel.
The inherent properties of stainless steel, such as its oxide layer and chemical composition, make it incompatible with the anodizing process.
When subjected to the anodizing process, stainless steel does not develop the desired porous oxide layer needed for dyeing or enhanced protection.
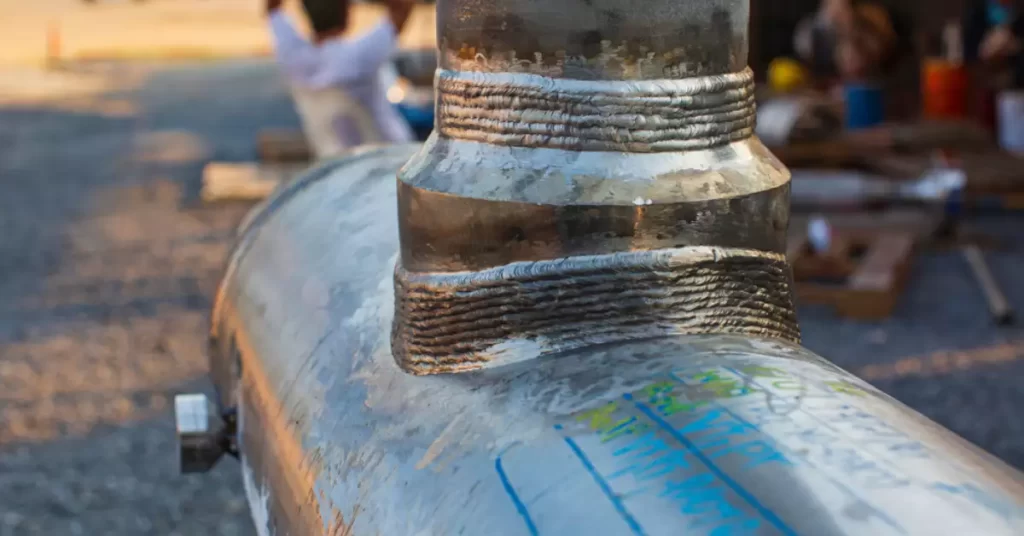
Alternative Methods for Coloring Stainless Steel
Although anodizing is not suitable for stainless steel, there are alternative methods to achieve a colored finish on this material.
Some of the most common methods include electrochemical coloring, heat coloring, and plating or coating.
Electrochemical Coloring
Electrochemical coloring, also known as electro coloring or INCO coloring, is a process similar to anodizing but specifically designed for stainless steel.
By immersing the stainless steel in a special electrolyte solution and applying an electric current, a thin oxide layer is formed on the surface.
This oxide layer produces a range of colors, including gold, bronze, blue, and black, depending on the voltage applied and the composition of the stainless steel.
The resulting finish is durable, corrosion-resistant, and maintains the natural luster of the base material.
Heat Coloring
Heat coloring, also known as temper coloring or heat tinting, involves heating the stainless steel to specific temperatures to produce a thin oxide layer that results in a variety of colors.
The color achieved depends on the temperature and duration of heating, with colors ranging from pale yellow to deep blue and even purple.
This method can be done using a torch, furnace, or specialized equipment.
However, it should be noted that heat coloring may affect the mechanical properties of the stainless steel and reduce its corrosion resistance, especially in harsh environments.
Plating and Coating
Plating and coating methods involve applying a thin layer of another material onto the surface of the stainless steel to achieve the desired color.
Common techniques include electroplating, powder coating, and PVD (Physical Vapor Deposition) coating.
Electroplating- Electroplating deposits a thin layer of metal, such as gold, silver, or chromium, onto the stainless steel surface. The resulting finish can be polished or matte, depending on the desired appearance.
Powder Coating- Powder coating involves applying a colored powder to the surface of the stainless steel, which is then heated to form a durable, corrosion-resistant finish. This method offers a wide range of colors and textures and is environmentally friendly.
PVD Coating- PVD coating uses a vacuum chamber to deposit a thin layer of metal, such as titanium, zirconium, or chromium, onto the stainless steel surface. This process produces a variety of colors, including gold, bronze, and rainbow, while maintaining the corrosion resistance and durability of the base material.
Applications of Colored Stainless Steel
Colored stainless steel is used in various industries and applications, including:
- Architecture and construction: Facades, wall cladding, roofing, and interior design elements.
- Automotive: Trim and decorative components, exhaust systems, and custom modifications.
- Consumer goods: Kitchen appliances, cookware, cutlery, and electronic devices.
- Jewelry and accessories: Watches, bracelets, and other fashion items.
- Medical and dental equipment: Instruments, implants, and tools.
Pros and Cons of Coloring Stainless Steel
Pros:
- Aesthetic appeal: Colored stainless steel adds a unique visual appeal to various products and applications.
- Enhanced durability: Some coloring methods, like electrochemical coloring and PVD coating, enhance the corrosion resistance and surface hardness of stainless steel.
- Customization: Coloring processes offer a wide range of colors, textures, and finishes to match specific design requirements.
Cons:
- Cost: Coloring processes can be more expensive than traditional stainless steel finishing techniques.
- Limitations: Some coloring methods may affect the mechanical properties of stainless steel or reduce its corrosion resistance.
Choosing the Right Process
Selecting the appropriate coloring method for stainless steel depends on factors such as budget, desired appearance, application requirements, and environmental conditions.
Each method has its advantages and disadvantages, and it is crucial to carefully consider these factors when deciding on the best option for a specific project.
FAQs
Q: Why can’t you anodize stainless steel?
A: The anodizing process is not suitable for stainless steel due to its inherent oxide layer and chemical composition.
Anodizing does not produce the desired porous oxide layer on stainless steel, making it incompatible with the process.
Q: What is the most durable method for coloring stainless steel?
A: PVD (Physical Vapor Deposition) coating is considered one of the most durable methods for coloring stainless steel.
It produces a thin, hard, and corrosion-resistant layer that maintains the base material’s properties while adding a vibrant and long-lasting color.
Q: Can heat coloring affect the corrosion resistance of stainless steel?
A: Yes, heat coloring can potentially affect the corrosion resistance of stainless steel, especially when exposed to harsh environments.
Heating the material can cause changes in its oxide layer and microstructure, potentially reducing its ability to resist corrosion.
Conclusion
In summary, while anodizing is not a suitable method for coloring stainless steel, there are several alternative techniques available, such as electrochemical coloring, heat coloring, and plating or coating.
These methods offer a wide range of colors, finishes, and durability for various applications. When selecting the appropriate coloring process, it is crucial to consider factors like budget, desired appearance, application requirements, and environmental conditions.
With the right method, it is possible to achieve stunning, colorful, and durable stainless steel products that meet specific design and performance needs.