Tool steels hold a special place in the world of metallurgy. Crafted with a focus on resisting wear, withstanding temperature changes, and displaying superior hardness, these materials are central to the world of manufacturing and production.
M2 and D2 are two distinct grades of tool steel. Each one carries a unique set of properties, proving useful in a variety of applications. The right choice between these two largely depends on the specifics of the job at hand.
Tool steels like M2 and D2 can significantly impact the efficiency of manufacturing processes. They serve as the backbone of many industries, including automotive, aeronautics, construction, and more.
M2 Tool Steel: An Overview
Definition and Properties
M2 tool steel, belonging to the high-speed steel (HSS) category, is renowned for its superior hardness and excellent wear resistance. It combines tungsten, molybdenum, and vanadium in its composition, leading to high heat resistance and toughness.
Common Uses and Applications
M2 tool steel is commonly used in the production of cutting tools, including drill bits and taps. Due to its high heat resistance, it’s also ideal for use in power-saw blades and other tools subjected to high heat during operation.
Advantages of M2 Tool Steel
M2 tool steel offers a slew of benefits. Its exceptional toughness ensures long-lasting tool life, while its high heat resistance makes it suitable for high-speed applications. Moreover, it can be machine-ground to a high polish, beneficial for certain tooling requirements.
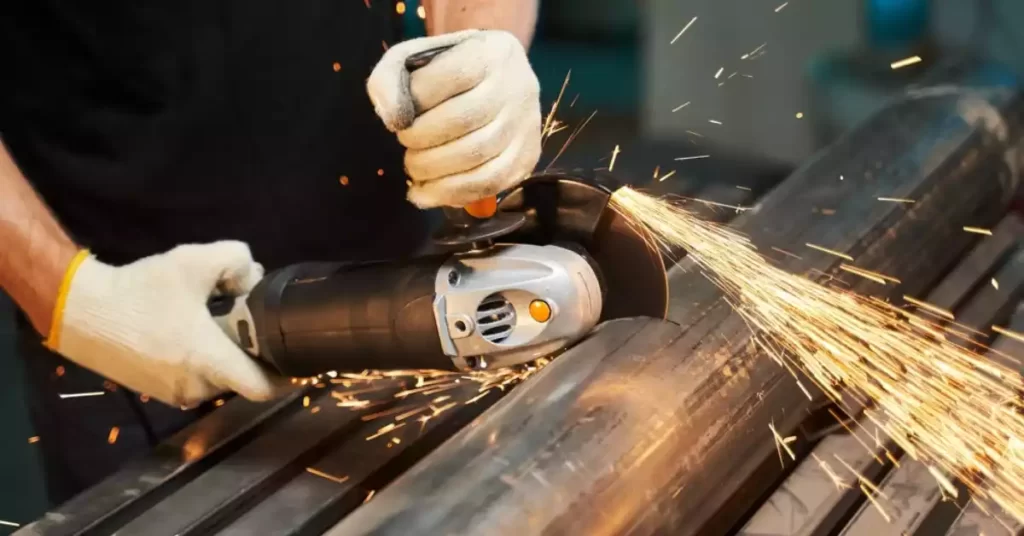
D2 Tool Steel: A Closer Look
Definition and Properties
D2 tool steel, part of the cold-work tool steel category, is characterized by its high carbon and chromium content. This unique composition gives it impressive hardness and wear resistance, albeit with less toughness than M2.
Common Uses and Applications
D2 tool steel finds its primary application in tools that require high wear resistance. Typical uses include blanking and forming dies, thread rolling dies, and knives and shears.
Benefits of D2 Tool Steel
The most prominent advantage of D2 tool steel lies in its high wear resistance, outperforming many other tool steels in this aspect. It also displays excellent dimensional stability during heat treatment, beneficial for precision tooling applications.
M2 vs D2 Tool Steel: Key Differences
Comparison of Chemical Composition
While both M2 and D2 tool steels offer impressive hardness and wear resistance, their chemical compositions differ significantly. M2, with its molybdenum, tungsten, and vanadium, exhibits excellent heat resistance. On the other hand, D2’s high carbon and chromium content contribute to its superb wear resistance.
Hardness and Durability Contrast
Both M2 and D2 possess superior hardness levels. However, M2’s hardness often comes paired with greater toughness, allowing for better resistance to cracking. D2’s hardness tends to accompany higher wear resistance but with less toughness.
Heat Treatment: M2 vs D2
The heat treatment processes for M2 and D2 also differ. M2’s heat resistance allows it to withstand higher tempering temperatures. In contrast, D2 requires careful heat treatment to achieve the best balance between hardness and toughness.
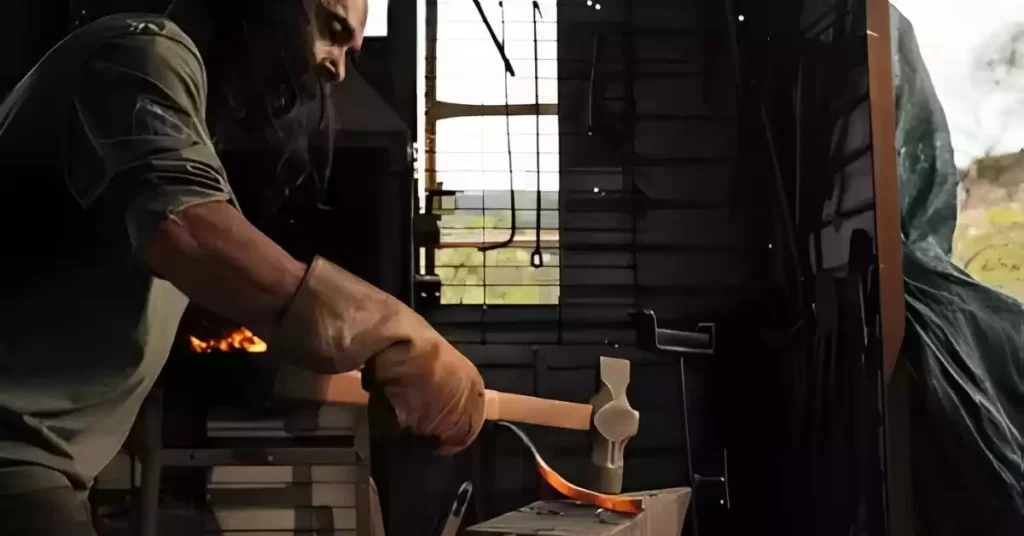
Cost Difference: An Analysis
Cost considerations also come into play when choosing between M2 and D2. While the costs fluctuate depending on the supplier and quantity, M2 usually comes at a premium due to its high-speed steel category.
Practical Performance in Various Applications
Lastly, practical performance can vary significantly between M2 and D2, depending on the application. M2 excels in high-speed, high-heat situations, while D2 shines in applications demanding high wear resistance and dimensional stability.
Selection Criteria: M2 or D2
Understanding Your Needs
The choice between M2 and D2 comes down to the specific requirements of your project. Understanding your needs is paramount in making the right selection.
Factors to Consider When Choosing
Several factors come into play when choosing between M2 and D2, including hardness, toughness, heat resistance, wear resistance, cost, and the specific tool application.
Real-world Examples and Case Studies
M2 Tool Steel in Action
In high-speed cutting applications, such as power saws and drill bits, M2 has proven its mettle repeatedly. Its hardness, heat resistance, and toughness make it an excellent choice for such demanding applications.
D2 Tool Steel at Work
For applications where wear resistance takes precedence over toughness, like in blanking dies, D2 has often been the tool steel of choice. Its impressive wear resistance ensures a longer tool life, contributing to increased efficiency.
Frequently Asked Questions
What Is the Main Difference Between M2 and D2 Tool Steel?
The main difference lies in their primary characteristics and applications. M2 is a high-speed steel known for its heat resistance and toughness, making it suitable for high-speed cutting tools. D2 is a cold-work tool steel valued for its high wear resistance, ideal for tools demanding durability and longevity.
Which Tool Steel Is More Expensive, M2 or D2?
Generally, M2 tool steel tends to be more expensive than D2 due to its category as a high-speed steel and its high molybdenum content.
Is D2 Tool Steel Tougher Than M2?
In terms of toughness, M2 tool steel typically outperforms D2. While D2 offers superior wear resistance, it does not match M2’s toughness, which allows it to resist cracking under pressure better.
Conclusion
Choosing between M2 and D2 tool steel boils down to the task at hand. M2’s heat resistance and toughness make it perfect for high-speed applications. On the other hand, D2’s superior wear resistance and dimensional stability fit the bill for tools where durability is paramount.
The journey through M2 and D2 tool steel showcases the variety and versatility inherent in tool steels. Both types have their specific strengths, reflecting the vast range of applications across various industries. It’s clear that understanding the properties and characteristics of these tool steels can play a significant role in improving manufacturing efficiency and productivity.
At the end of the day, the choice between M2 and D2 tool steel depends on the specific requirements of the project. By matching the right steel to the job, you can optimize your manufacturing process and achieve the best possible results.