We’ve all been there—attempting to tighten a screw in a hole, only to realize that it keeps spinning endlessly. Stripped screw holes in metal can be a frustrating problem, but fear not!
With the right tools and techniques, you can quickly and easily repair these pesky imperfections.
In this guide, we’ll walk you through the process of fixing a stripped screw hole in metal, from understanding the issue to implementing the most effective solutions.
Understanding Stripped Screw Holes in Metal
Causes of Stripped Screw Holes
Stripped screw holes occur when the metal threads inside the hole become damaged or worn out. This can happen due to:
- Over-tightening of the screw
- Using the wrong size or type of screw
- Frequent removal and reinstallation of the screw
- Poor quality metal
Consequences of Ignoring Stripped Screw Holes
If left unaddressed, stripped screw holes can lead to:
- Reduced structural integrity
- Loosening of components
- Possible damage to the surrounding metal
Tools and Materials Required
Before you start fixing a stripped screw hole, gather the following tools and materials:
- Screwdriver or drill
- Larger screw (if applicable)
- Metal filler or epoxy
- Tap and die set
- Helicoil or threaded insert
- Wrench
- Safety goggles
Methods to Fix a Stripped Screw Hole in Metal
There are several methods to fix a stripped screw hole in metal. The most appropriate method depends on the specific situation and the tools and materials available.
Using a Larger Screw
This is the simplest method for fixing a stripped screw hole. Simply replace the original screw with a slightly larger one that can grip the remaining threads. Make sure the new screw is compatible with the hole and the material it is securing.
Filling the Hole with a Metal Filler
Using a metal filler or epoxy, you can create a new, solid base for the screw. Apply the filler according to the manufacturer’s instructions, and let it cure completely before drilling a new hole and reinserting the screw.
Retapping the Hole
Retapping involves cutting new threads into the existing hole. Using a tap and die set, carefully create new threads that match the size and pitch of the original screw.
Inserting a Helicoil
A Helicoil is a small, coiled wire insert that can be threaded into a stripped hole. Once in place, the Helicoil provides new, strong threads that can hold the original screw securely.
Using a Threaded Insert
Similar to a Helicoil, a threaded insert is a small metal sleeve that can be installed into the stripped hole.
The insert has internal threads that match the original screw and external threads that grip the surrounding metal.
Threaded inserts are typically more robust than Helicoils and are suitable for heavy-duty applications.
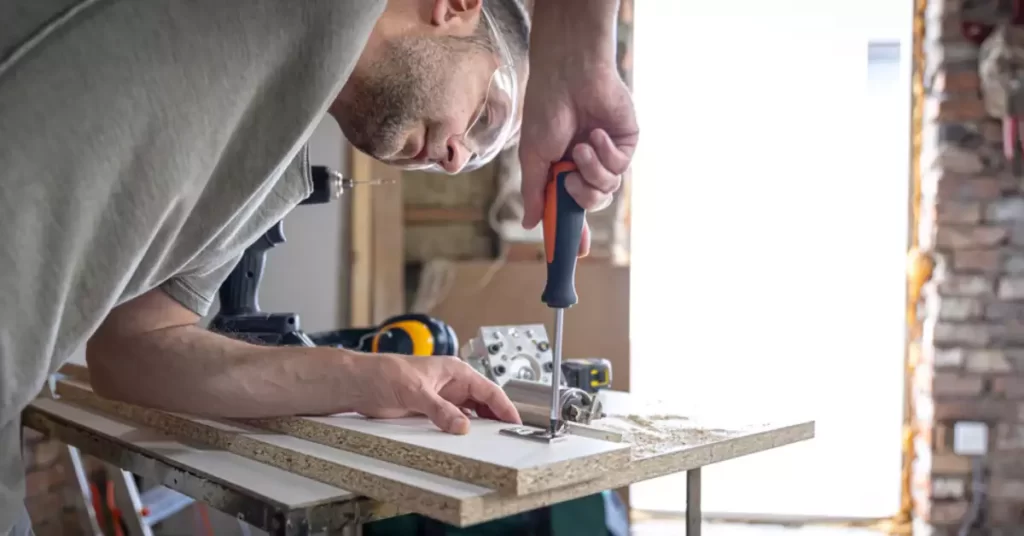
Detailed Explanation of Each Method
Using a Larger Screw
Select the appropriate screw: Choose a screw that is slightly larger in diameter than the original one. Ensure that the new screw is compatible with the material it is securing and has the correct thread pitch.
Remove the damaged screw: Carefully remove the damaged screw from the hole using a screwdriver or drill.
Clean the hole: Use a wire brush or compressed air to remove any debris or loose metal from the hole.
Install the larger screw: Align the new screw with the hole and carefully tighten it into place. Avoid over-tightening the screw, as this can cause additional damage.
Filling the Hole with a Metal Filler
Choose the right metal filler: Select a metal filler or epoxy that is specifically designed for use with metals. Check the manufacturer’s instructions to ensure compatibility with your specific metal type.
Prepare the hole: Remove the damaged screw and clean the hole using a wire brush or compressed air.
Mix the filler: Follow the manufacturer’s instructions for mixing the metal filler or epoxy.
Apply the filler: Carefully apply the filler to the stripped screw hole, ensuring that it fills the entire hole.
Allow the filler to cure: Follow the manufacturer’s instructions for curing time. This step is crucial, as the filler must harden properly to provide a solid base for the screw.
Drill a new hole: Once the filler has cured, use a drill bit that matches the size of the original screw to create a new hole in the filled area.
Reinstall the screw: Align the screw with the new hole and tighten it securely without over-tightening.
Retapping the Hole
Gather tools: Obtain a tap and die set that matches the size and thread pitch of the original screw.
Remove the damaged screw and clean the hole: Use a screwdriver or drill to remove the screw, and clean the hole with a wire brush or compressed air.
Select the correct tap: Choose a tap from the set that matches the original screw’s size and thread pitch.
Apply cutting fluid: Apply a small amount of cutting fluid to the tap and the hole to reduce friction and prevent damage.
Align the tap: Carefully align the tap with the hole, ensuring that it is straight and properly positioned.
Cut new threads: Slowly turn the tap clockwise while applying gentle pressure. As you cut new threads, periodically back the tap out slightly to clear any debris.
Clean the hole: Once the new threads have been cut, remove the tap and clean the hole of any debris or cutting fluid.
Reinstall the screw: Insert the original screw into the newly tapped hole and tighten it securely without over-tightening.
Inserting a Helicoil
Choose the appropriate Helicoil kit: Select a Helicoil kit that matches the size and thread pitch of the original screw.
Drill out the hole: Using the provided drill bit from the kit, drill out the stripped hole to the specified size.
Tap the hole: Using the provided tap from the kit, create new, larger threads in the hole.
Install the Helicoil: Thread the Helicoil onto the provided installation tool and insert it into the newly tapped hole. Turn the tool clockwise until the Helicoil is fully seated.
Remove the installation tool: Unscrew the installation tool from the Helicoil, leaving the Helicoil in place.
Reinstall the screw: Thread the original screw into the Helicoil and tighten it until it is secure.
Step-by-Step Guide to Fixing a Stripped Screw Hole
Assess the situation: Determine the extent of the damage and select the most appropriate method for fixing the stripped screw hole.
Gather tools and materials: Assemble the necessary tools and materials based on the chosen method.
Remove the screw: If it’s still in the hole, carefully remove the damaged screw using a screwdriver or drill.
Clean the hole: Remove any debris, dirt, or loose metal from the hole using a wire brush or compressed air.
Apply the chosen method: Follow the instructions for the chosen method (larger screw, metal filler, retapping, Helicoil, or threaded insert) to repair the stripped screw hole.
Reinstall the screw: Once the repair is complete, reinstall the original screw or a suitable replacement, ensuring that it’s properly tightened without over-tightening.
Preventive Measures to Avoid Stripped Screw Holes
To minimize the risk of stripping screw holes in metal, consider the following preventive measures:
- Use the correct size and type of screw for the application.
- Avoid over-tightening screws; use a torque wrench if necessary.
- Periodically check screws for signs of wear or damage.
- Use high-quality screws and metal components.
Common Mistakes to Avoid
When fixing a stripped screw hole, avoid these common mistakes:
Rushing the process: Take your time to assess the situation, gather the necessary tools and materials, and perform the repair correctly.
Over-tightening the screw: This can cause additional damage to the hole and the surrounding metal.
Ignoring signs of wear or damage: Regularly inspect screws and metal components for signs of wear or damage, and address issues as they arise.
When to Seek Professional Help
If you’re unsure of your ability to fix a stripped screw hole in metal, or if the damage is extensive or in a critical location, consult a professional. They have the experience and tools necessary to repair the issue safely and effectively.
Frequently Asked Questions (FAQs)
Q1: Can I use any type of metal filler to fix a stripped screw hole?
A: It’s important to use a metal filler or epoxy that is specifically designed for use with metals. Check the manufacturer’s instructions to ensure compatibility with your specific metal type.
Q2: How do I know if I need to use a Helicoil or a threaded insert?
A: The choice between a Helicoil and a threaded insert depends on the specific application and the amount of load the screw will bear.
Helicoils are typically more suitable for lighter loads, while threaded inserts are better for heavy-duty applications.
Q3: Can I retap a hole without a tap and die set?
A: A tap and die set is the most appropriate tool for re tapping a hole, as it ensures that the new threads are accurately cut and properly aligned.
Attempting to retap a hole without the proper tools can result in further damage to the hole and the surrounding metal.
Final Verdict
Fixing a stripped screw hole in metal is a common but manageable issue. By assessing the situation, selecting the most appropriate method, and using the proper tools and techniques, you can restore the functionality of the screw hole with minimal fuss.
Always remember to take preventive measures to avoid stripped screw holes in the future and consult a professional if you’re unsure of your ability to repair the issue yourself.