Stainless steel has several varieties and 440C stands out as a popular choice for many industrial and commercial applications. Renowned for its durability, corrosion resistance, and impressive hardness after heat treatment, this grade of steel is a top choice for applications that demand exceptional performance.
440C stainless steel is a high-carbon chromium steel designed to provide stainless properties with maximum hardness. It achieves this remarkable hardness during a heat treatment process, which notably improves its mechanical properties.
This grade of steel plays a critical role in various industries, from the production of high-end knives and cutting tools to high-quality surgical instruments. Its ability to withstand intense environments and maintain excellent performance makes it a staple material in these demanding applications.
Importance of Heat Treatment in Metals
Heat treatment is a vital aspect of metallurgical processes. It has the capability to alter the physical, and sometimes chemical, properties of a material – in this case, 440C stainless steel.
The Role of Heat Treatment
Heat treatment manipulates the structure of the steel, refining its grain size, and optimizing its properties. For 440C stainless steel, it increases hardness and improves the resistance to wear and tear, enhancing the steel’s overall performance.
Benefits of Heat Treatment on 440C
Through heat treatment, 440C stainless steel gains heightened mechanical strength and improved durability. It offers an increased ability to withstand high-stress environments, making it an ideal choice for various industries.
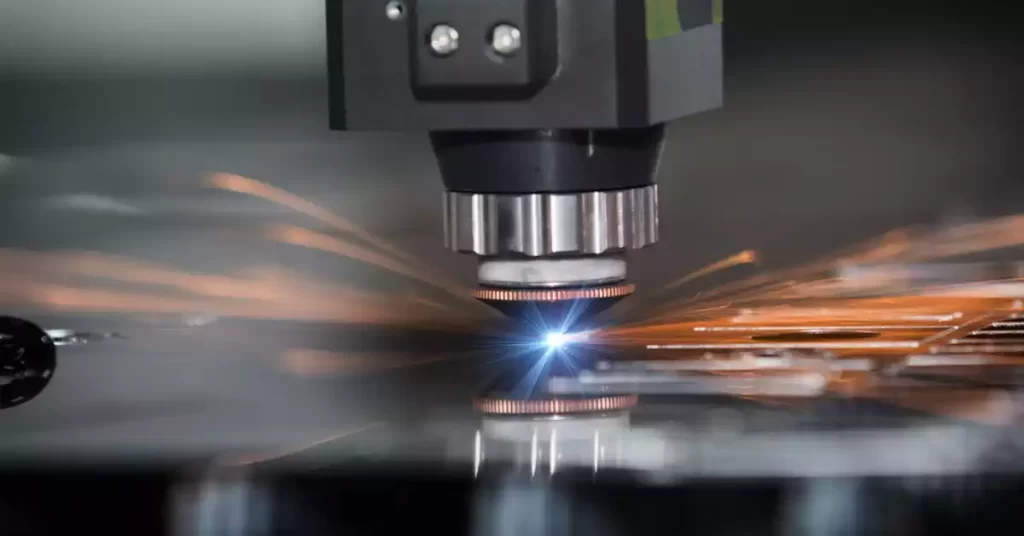
Overview of 440C Heat Treatment
440C heat treatment is an intricate process, vital for improving the steel’s mechanical properties. It imparts improved hardness and strength to the steel.
Definition and Purpose of 440C Heat Treatment
440C heat treatment refers to the process of heating and cooling the steel under controlled conditions to alter its physical properties. The process is critical for enhancing the hardness and strength of 440C stainless steel.
Impact on 440C Stainless Steel
Through heat treatment, 440C stainless steel’s hardness dramatically improves, resulting in excellent wear resistance. Moreover, the process also enhances its resistance to corrosion, making it more suitable for applications in corrosive environments.
Heat Treatment Process of 440C
The process of 440C heat treatment is complex and involves several crucial phases. Each of these phases contributes to the final hardness, toughness, and resistance properties of the steel.
Preheating Phase
The heat treatment process begins with preheating. During this stage, the 440C stainless steel is heated evenly to a specific temperature. This temperature is typically lower than that of the main hardening phase. Preheating is a preparatory stage, helping to prevent structural defects, such as cracking, that could occur if the steel were to be directly exposed to the high temperatures of the hardening phase.
During preheating, the heat is applied gradually. This helps ensure uniform heating, preparing the steel for the austenitizing phase. The preheating phase can be broken down into two or three steps, depending on the specific heat treatment requirements.
Austenitizing Phase
Following preheating is the austenitizing phase. In this stage, the steel is heated to a much higher temperature. This temperature causes the steel’s structure to change and form austenite. The austenitizing temperature for 440C stainless steel is typically around 1010-1065°C (1850-1950°F).
Austenitizing is the core of the heat treatment process, as it significantly influences the final hardness of the steel. The temperature and time duration for which the steel is held at this stage can vary based on the desired hardness and other specific application requirements.
Quenching Phase
After the austenitizing phase comes quenching. Quenching involves rapidly cooling the steel from the austenitizing temperature. This rapid cooling, or quenching, “freezes” the steel’s structure, locking in the hardness achieved during the austenitizing phase.
The quenching process can be performed using various mediums such as oil, air, or water. The choice of quenching medium depends on the type of steel and the required properties. For 440C stainless steel, air and oil are commonly used.
Quenching also induces stresses in the steel due to the rapid change in temperature. These stresses can lead to structural changes and potential cracking or warping of the steel, which brings us to the next important phase: tempering.
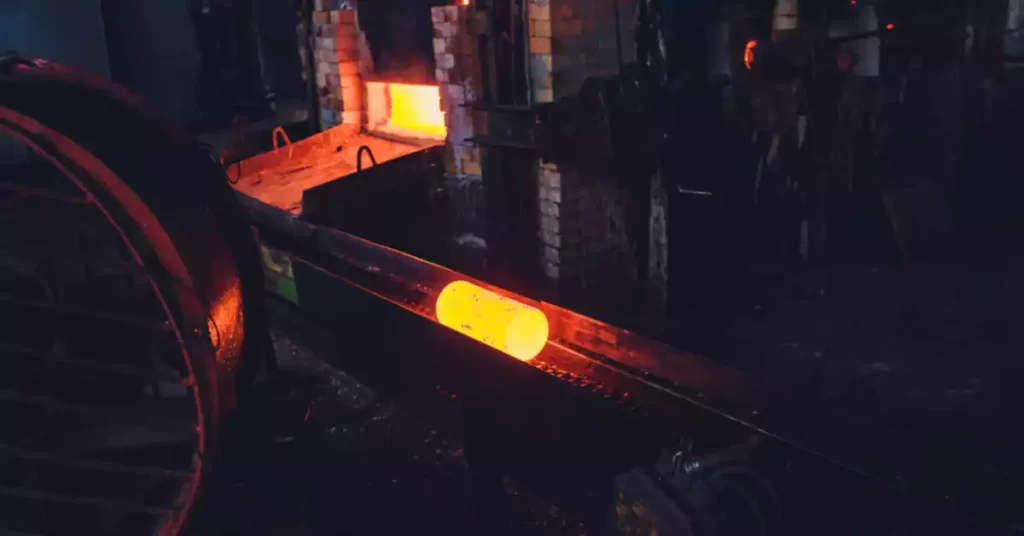
Hardening of 440C Stainless Steel
The primary goal of heat treating 440C stainless steel is to enhance its hardness and strength, a process known as hardening.
Explanation of the Hardening Process
Hardening involves the transformation of the steel structure through controlled heating and cooling. The steel is first heated to its austenitizing temperature. Then, it’s soaked at that temperature to ensure the formation of austenite. Finally, the steel is rapidly cooled, or quenched.
The rapid cooling causes the austenite to transform into martensite, a hard and brittle phase. It’s this martensitic structure that gives 440C stainless steel its hardness.
Benefits of Hardening 440C Stainless Steel
By hardening 440C stainless steel, several mechanical properties are enhanced. The most significant of these is the steel’s hardness. Hardened 440C stainless steel exhibits excellent wear resistance, making it ideal for tools and parts that need to withstand high friction without deforming.
In addition, hardening also enhances the steel’s tensile strength and yield strength. These properties make it capable of withstanding high stresses and deformations, further expanding the applications of 440C stainless steel.
Tempering of 440C Stainless Steel
Once hardened, the 440C stainless steel can be quite brittle. This brittleness can make it prone to chipping or cracking under extreme conditions. To alleviate this brittleness and improve its toughness, a process known as tempering is applied.
Understanding Tempering
Tempering involves reheating the hardened steel to a temperature below the austenitizing temperature. This heating and controlled cooling process results in the precipitation of iron carbides from the martensite, which softens the steel.
While tempering does decrease hardness, it significantly increases the toughness of 440C stainless steel. The reduced brittleness makes the steel more durable and capable of withstanding high impact loads without failing.
Importance of Tempering in Heat Treatment
Tempering plays a crucial role in balancing the hardness and toughness of 440C stainless steel. Without tempering, the hardened steel may be too brittle for practical use. With tempering, the steel becomes less brittle, more durable, and more suitable for a wide range of applications.
The choice of tempering temperature depends on the desired balance between hardness and toughness. Higher tempering temperatures result in greater toughness but lower hardness, and vice versa.
Typically, for 440C stainless steel, a tempering temperature range of 149-204°C (300-400°F) is used for applications that require a high hardness level, while a range of 204-316°C (400-600°F) is used for a balanced combination of hardness and toughness.
Case Studies: 440C Heat Treatment in Industries
Heat-treated 440C stainless steel is used in a variety of industries due to its enhanced mechanical properties. Here are a couple of notable examples.
Usage of 440C Heat Treatment in Aviation Industry
In the aviation industry, 440C heat-treated stainless steel is used for manufacturing parts that need to withstand high stress and corrosion. These can include bearings and high-grade fasteners. The exceptional hardness and corrosion resistance of 440C make it an ideal choice for these critical components.
Application in Medical Instruments Manufacturing
In the medical industry, heat-treated 440C stainless steel is used for manufacturing surgical instruments. The high hardness of the steel, combined with its excellent corrosion resistance, makes it suitable for producing durable, long-lasting instruments that can withstand repeated sterilization processes.
Tips for Successful 440C Heat Treatment
There are several key points to consider when carrying out a 440C heat treatment process. Here are a few tips for achieving successful results.
Preparation Tips
- Ensure the 440C stainless steel is clean and free from contaminants before starting the heat treatment.
- Preheat the steel gradually to prevent thermal shock and structural defects.
- Carefully control the austenitizing temperature and time to achieve the desired hardness.
Common Mistakes to Avoid
- Avoid uneven heating during the austenitizing phase. This can lead to non-uniform hardness in the final product.
- Be careful not to overheat the steel during the austenitizing phase as this can cause excessive grain growth, leading to reduced toughness.
- After quenching, don’t delay the tempering process. Delaying can result in stresses leading to cracking.
Frequently Asked Questions
What is the ideal austenitizing temperature for 440C stainless steel?
The ideal austenitizing temperature for 440C stainless steel typically lies between 1010-1065°C (1850-1950°F). However, the specific temperature can vary depending on the desired hardness and other application requirements.
Why is quenching necessary in the heat treatment process?
Quenching is necessary to “freeze” the structural changes that occur in the steel during the austenitizing phase. Rapid cooling prevents the newly formed austenite from reverting to its original structure, resulting in a much harder steel.
What is the purpose of tempering after hardening?
The main purpose of tempering after hardening is to reduce the brittleness of the steel. While hardening increases the hardness and strength of the steel, it also makes it very brittle. Tempering helps alleviate this brittleness, making the steel tougher and more durable.
Conclusion
In the world of stainless steel, 440C has earned its place as a high-performing variant thanks to its unique composition and the transformation it undergoes during heat treatment. This process, consisting of preheating, austenitizing, quenching, and tempering, significantly enhances the mechanical properties of the steel.
The result of this intricate process is a material that’s incredibly hard, resistant to wear, and capable of withstanding high-stress environments. This makes it a favorite in industries such as aviation, medical instruments manufacturing, and many more.
Ultimately, heat treatment is a delicate process, and successful execution requires precision, knowledge, and careful control of various factors. The rewards, however, are great – producing a variant of stainless steel that outperforms many others in terms of hardness and durability.